
In the intricate world of industrial operations, precision and safety are non-negotiable. Our commitment to delivering cutting-edge solutions is embodied in our in-house manufactured Purge Panel – a technological marvel designed to elevate your manufacturing processes. In this blog post, we will delve into the technical specifications that make our Purge Panel stand out and how the in-house manufacturing process adds a layer of customization and quality assurance to ensure optimal performance.
Decoding Efficiency: Technical Marvels of Our In-House Manufactured Purge Panel
Intricacies of In-House Manufacturing:
Our journey began in 1999 with a vision to provide efficient, reliable and sustainable Solutions for Increasingly complex Industrial Solutions the vision was foreseen and implemented with our in-house manufacturing facility, where every Purge Panel is meticulously crafted to meet the highest industry standards. From the initial design phase to the final quality checks, our team of experts ensures that each component aligns with our commitment to excellence.
The Aim of developing this State-of-the-art facility is to cater every possible Industry and providing customer-centric Integrated Solutions.
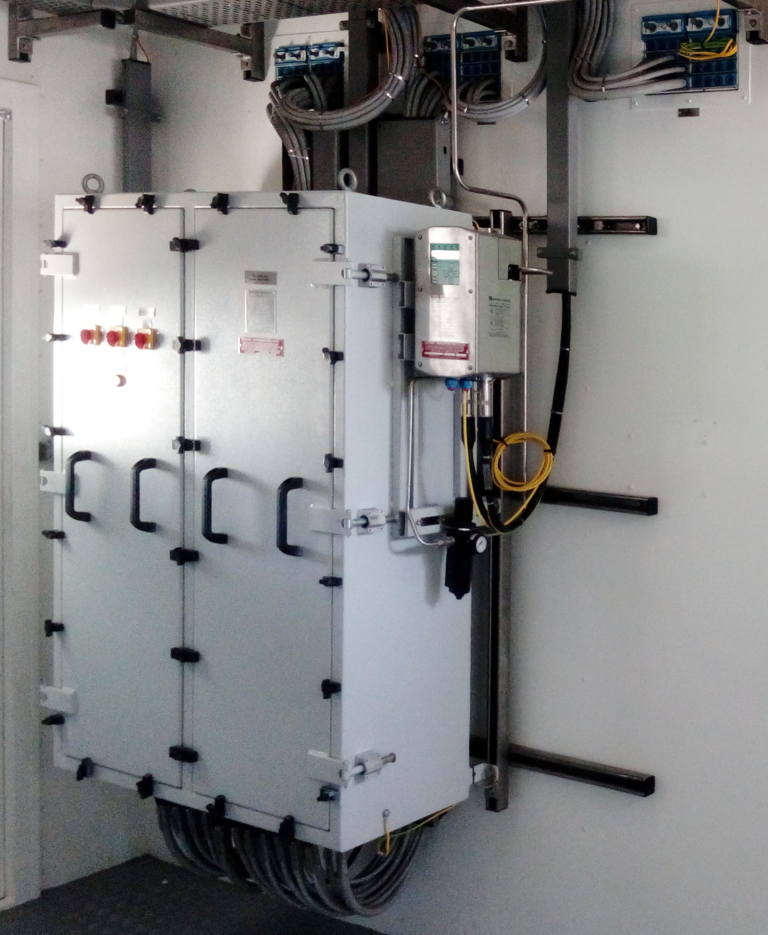
Design and Architecture:
Enclosure Material and Design
The heart of our Purge Panel lies in its enclosure – constructed from robust materials to withstand the harshest industrial environments. Our in-house manufacturing process allows us to customize enclosure designs, ensuring they seamlessly integrate with your specific operational needs while maintaining the highest standards of durability. The in-house manufacturing process enables us to tailor these systems to your industry’s specific requirements, providing precise control over the purging sequence and ensuring optimal safety levels.
Control System Architecture
At the core of our Purge Panel is a sophisticated control system designed for precision and reliability. With a PLC/other control Panel based architecture, our panels provide unparalleled control over purge and pressurization sequences. The in-house manufacturing approach allows us to adapt the control system to your unique specifications, ensuring it aligns seamlessly with your existing industrial setup.
Purge and Pressurization System
Our Purge Panels are equipped with state-of-the-art purge and pressurization systems, designed to create a safe environment in hazardous areas.
Temperature and Moisture Controls
In industrial settings, maintaining the right temperature and Moisture levels is crucial. Our Purge Panels come equipped with advanced temperature and Moisture control features. The in-house manufacturing advantage allows us to fine-tune these controls to match the unique environmental conditions of your facility, ensuring optimal operational efficiency.
Integration with Industrial Networks:
Connectivity is key in modern industrial setups. Our Purge Panels seamlessly integrate with industrial networks through various communication protocols. In-house manufacturing allows us to customize these integration options, ensuring compatibility with your existing control and monitoring systems.
Types of Purge Panel offered:
Single-stage pressure regulators may not be suitable for applications where the gas supply pressure is unstable or where precise gas flow control is necessary. They are also not recommended for applications that require very low or very high output pressures.
Purge Panel for Zone 1 / Zone 2 – Our Purge Panel is purpose-built to meet the stringent requirements of Zone 1 (constant hazard) and Zone 2 (occasional hazard) areas, ensuring safe operations in environments with potentially explosive atmospheres. PESO and ATEX certified purge controller used according to the area classification.
Purge Panel with Ex AC – IP65 – Our Ex AC – IP65 Purge Panel is an intrinsically safe solution, combining Ex AC (intrinsically safe alternating current) certification with an IP65 ingress protection rating. Designed for hazardous environments, it ensures secure operation in explosive atmospheres while providing robust protection against dust and water ingress. With advanced purge and pressurization systems, rugged construction, and user-friendly features, this panel stands as a reliable safeguard in industrial settings where safety and operational integrity are top priorities.
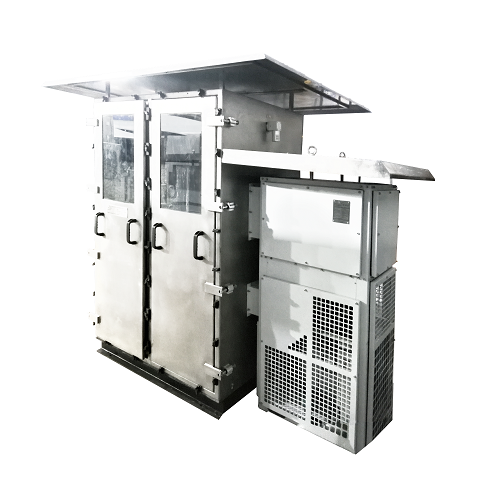
Purge Panel with Vortex Cooler – Our Purge Panel, enhanced with a Vortex Cooler, is a cutting-edge solution designed for hazardous environments. The Vortex Cooler technology efficiently cools the enclosure by utilizing compressed air, preventing overheating and ensuring optimal conditions for sensitive equipment. This integration enhances safety and extends the lifespan of critical components, making it an ideal choice for industries where temperature control is paramount.
Features
- Purge Panel have pressure withstanding capacity as per design.
- Hydro Carbon accumulation are taken care
- Moisture free purge is desired
- Electrostatic discharge is one of the major features.
- Various sizes for accommodating various equipments.
- Purge Panel with Ex-AC – IP65 certification.
Conclusion:
Incorporating our in-house manufactured Purge Panel into your industrial setup means embracing a solution tailored to your specific needs. The technical specifications discussed above reflect our dedication to precision, safety, and efficiency. With the flexibility and customization options afforded by our in-house manufacturing process, our Purge Panel becomes not just a product but a bespoke solution crafted to elevate your industrial processes to new heights of excellence.